The History Of The Automatic Forklift
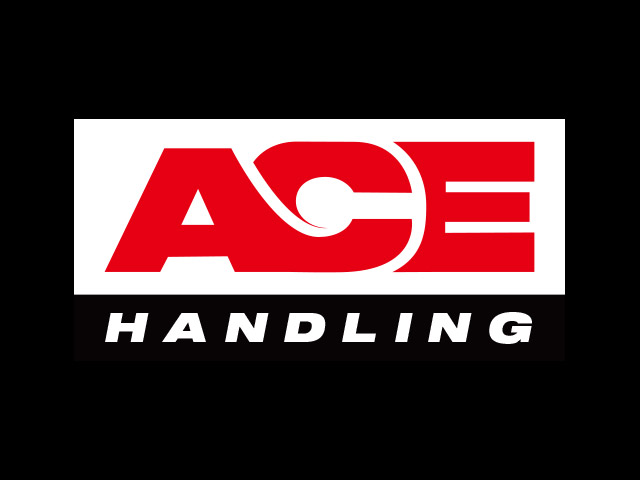
A robust, hardworking forklift hire is a fundamental part of any warehouse, dockyard or construction site, and because of this, there are more than a few tributes to the vehicle that made the modern warehouse in the rather unexpected world of computer games.
In nearly every work environment, skilled, trained operators are in charge of driving vehicles that are very important but also need to be taken care of to ensure safe operation.
However, some businesses have adopted the use of automated guided vehicles (AGVs) such as automatic forklifts in fields such as warehousing, manufacturing and paper-and-print, where heavy materials need to regularly be transported across a large building.
They are often conflated with robot forklifts, but whilst the two are similar in that they both can complete relatively simple tasks without direct assistance or guidance, they are fundamentally different in the way they complete these tasks.
Robot forklifts rely on artificial intelligence and information processing that allows them to complete tasks autonomously by mapping the local area and sensing where it is.
AGVs, on the other hand, are simpler and follow a rigid route provided using either guiding tape, magnetic sensors, wires or lasers that the forklift follows carefully, and can in some cases provide other instructions, such as waiting for a load, unloading, raising and lowering forks.
The concept of the AGV was initially implemented by Barrett Electronics in 1953, a company based in Northbrook, Illinois, which consisted of a tow truck that would be attached to a wire in the floor rather than a rail, allowing it to be operated automatically.
This proved to be popular and spread rapidly throughout the 1960s, with the initial wires being replaced by magnetic tape, then guide tape and more commonly laser target navigation.
Whilst the technology is effective at simple tasks, part of the reason why they have not completely supplanted the manned operator in many warehouses is partly due to initial investment but mostly due to the complex nature of even a controlled environment such as a warehouse.
Artificial intelligence is the next step in automatic forklifts but as has been seen in the world of self-driving cars, there is a long way to go before they will truly supplant human operators.
Part of the reason for this is that we give ourselves way too little credit for our ability to adapt to unexpected situations.
The road, in particular, is filled with potential hazards and changes, such as elevation changes, road condition factors, children running into the road and different traffic levels to consider.
Even in a warehouse, there are potential unexpected hazards, particularly if there is a mix of human and machine operated lift trucks and people travelling through it, and whilst lighting and large parts of the work environment can be controlled, AI models are still not the best at improvising and applying knowledge generally.
However, unlike self-driving cars, where the number of edge cases will make their widespread application a long process even once a suitably adaptive AI emerges, many of the issues surrounding AI-driven forklifts can be overcome with careful warehouse design.